"La crise des semi-conducteurs ou la nécessaire révision des pratiques d'achats"
KPMG France vient de publier une étude qui analyse la crise des semi-conducteurs ainsi que ses origines, et donne des pistes pour éviter les crises à répétition. Entretien avec Frédéric Thielen, expert achats chez KPMG.
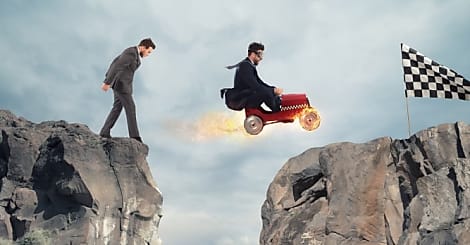
La crise des semi-conducteurs aurait-elle pu être anticipée et donc, minorée... voire évitée?
Elle aurait pu être minorée pour trois raisons. Deux raisons indépendantes du secteur automobile et une troisième, propre au secteur. La première chose est que la gestion des risques fournisseurs est actuellement trop statique. Nous en avions d'ailleurs parlé lors de deux webinars faits ensemble (voir le replay du webinar Après Covid : quelle politique achats ? et le replay du webinar La gestion dynamique des risques fournisseurs). Elle est souvent gérée sous la forme d'une matrice revisitée tous les six mois/un an. L'approche doit être plus dynamique. J'ai la conviction qu'une analyse des risques doit être plus imbriquée dans le processus de gestion de risques au quotidien. Le deuxième facteur est le fait que les directions achats sont très focalisées sur les fournisseurs de rang 1, ce qui est ici un vrai souci puisque, dans le cas des semi-conducteurs, la difficulté vient de fournisseurs de rang 3, 4 et 5, qui impactent les fournisseurs de rang 1. Il est certes difficile de capter ses fournisseurs jusqu'au rang 5 et je pense même que ce n'est pas gérable, parce qu'en plus, cela change tout le temps.Mais l'idée est d'améliorer la visibilité en captant des tendances de marché et des signaux faibles qui concernent le secteur dans lequel évoluent ces fournisseurs. Ceci pour comprendre les dynamiques de marché et mieux s'y adapter. Ces deux points sont multisectoriels. La troisième raison est, à mon sens, plus spécifique à l'industrie automobile.
Quelles sont donc les spécificités liées au secteur automobile ?
Cette troisième raison est clairement un sujet d'évolution des produits. Les constructeurs sont en train d'électrifier leurs gammes, et leurs besoins en électronique et en semi-conducteurs augmentent de fait. Sur un véhicule électrique, il y en a pour environ 300 dollars de semi-conducteurs et cela est encore plus flagrant si on parle de véhicules connectés et autonomes. Là, on monte plutôt à 3000 dollars de semi-conducteurs dans un véhicule. Or, la demande en véhicules électriques ne fait qu'augmenter. On arrive déjà à des ratios d'immatriculation supérieurs à 50% dans certains pays d'Europe. Les gammes constructeurs changent et les produits qu'ils utilisent changent aussi. Jusqu'à il y a peu, l'industrie automobile représentait 8% environ du marché des semi-conducteurs. Pour les fabricants de semi-conducteurs, l'automobile était en quatrième ou cinquième place par ordre d'importance. Devant eux, l'informatique, les serveurs, les télécoms. Ils ne sont pas encore les clients privilégiés des fabricants de semi-conducteurs.
Le big data aurait-il pu aider à prévoir la pénurie?
Le big data n'est qu'un des outils de la gestion dynamique du risque fournisseur, qui passe aussi par d'autres modalités. Mais un système de gestion dynamique des risques permet de remonter les signaux faibles en avance de phase pour avoir une meilleure vue d'ensemble. Si la filière automobile dans sa globalité avait pu mieux anticiper que la 5G, par exemple, allait augmenter le besoins en composants, elle aurait peut être réagi différemment. Il faut savoir saisir les signaux faibles sur le marché de matières premières et les marchés fournisseurs de rangs 3, 4 et 5 car ils risquent d'impacter les fournisseurs de rang 1.
Vous dites que les donneurs d'ordre du secteur auto doivent changer leur mode de relation avec ces fournisseurs de semi-conducteurs.... mais que faut-il changer?
Les concurrents à l'achat de semi-conducteurs dont nous venons de parler n'ont pas les mêmes modes de relation avec leurs fournisseurs. Ils ont des habitudes de travail plus anciennes et établies. De fait, les fabricants sont capables de faire des plans d'investissements en conséquences. Les acheteurs de l'automobile sont alors confrontés au fait que non seulement ils représentent encore une part limitée des besoins, mais aussi qu'ils n'ont pas nécessairement tous les codes. Actuellement, dans l'automobile, nous avons souvent des constructeurs et des équipementiers qui sont en place depuis des années et qui produisent ensemble des véhicules thermiques depuis des années. Ils ont appris à fonctionner de concert et s'adaptent les uns aux autres. Le même apprentissage devient sans doute nécessaire, dans ce contexte d'électrification.
Sur quoi la relation peut-elle achopper?
Sur beaucoup de choses, comme dans une relation client-fournisseur, mais sans doute et surtout sur le rebouclage capacitaire. En fonction des prévisions que leur donnent leurs clients, les fabricants prévoient leurs investissements. Si je suis fabricant, que je ne suis pas habitué à travailler avec l'automobile, que je reçois des projections de différents secteurs à la fois et que je me demande quel est mon niveau d'incertitude de ce qui est annoncé, je vais minorer mon plan d'investissement pour ne pas prendre de risques. Cette difficulté-là, l'affermissement des prévisions, est un sujet d'appréciation des fournisseurs sur la capacité de production à mettre en place.
Il faut acquérir de nouveaux réflexes. Repenser nos logiques de supply chain, en particulier dans l'automobile, très influencée par le lean, ce qui n'est pas le cas des autres industriels qui sont plus sur une logique d'allocation des capacités et des stocks. Or le lean, c'est bien, mais pas partout ni tout le temps. Le lean fonctionne bien lorsqu'il n'y a pas de risques.
Il y a également un sujet d'apprentissage de la supply chain jusqu'à un niveau plus bas afin d'éviter le mono-sourcing. Tel constructeur, pour un véhicule donné, peut encore mettre jusqu'à un niveau cinq des fournisseurs en mono-source sur un véhicule donné. Parce que ce véhicule, quoique représentant beaucoup pour lui en termes d'image, n'a de son point de vue pas suffisamment de volume pour justifier de doubles sources. Auquel cas, il est alors tributaire d'une ligne de 4 ou 5 fournisseurs en mono-source et... dès qu'un fournisseur lâche, c'est tout le véhicule qui lâche.
Lire la suite en page 2 : Qu'est ce qui fait que certains constructeurs ont été moins impactés que d'autres dans un premier temps? / Vous anticipez d'autres risques... quels devraient être les autres points de vigilance actuels? / Savez-vous s'il y a des projets de relocalisation qui concernent la production de semi-conducteurs? / Les constructeurs européens pourraient-ils envisager de créer une JV pour financer la création d'une usine de semi-conducteurs? / Que conseillez-vous actuellement à vos clients impactés par la crise des semi-conducteurs ou autre pénurie?
Qu'est ce qui fait que certains constructeurs ont été moins impactés que d'autres dans un premier temps?
Sans doute parce qu'ils ont réagi plus vite ou parce que qu'ils ont une supply chain géographiquement plus proche. Ford a pour sa part eu une réponse plus inattendue. Le constructeur a décidé d'enlever des cartes électroniques de certains de ses véhicules aux Etats-Unis, pour continuer à en produire au même rythme. Il a ôté des cartes qui permettaient d'optimiser la consommation d'essence, et l'a publiquement assumé.
Il y aura probablement une amélioration de cette pénurie en fin d'année parce qu'il y a une saisonnalité de la production des appareils électroniques grand public, très gourmands en semi-conducteurs. Les stocks se font deux à trois mois avant les fêtes de fin d'année. Pour autant, la constitution de capacités de production adéquates sera de plus longue haleine, de l'ordre de 2 ans.
Vous anticipez d'autres risques... quels devraient être les autres points de vigilance actuels?
Les matières plastiques, mais sans doute pas toutes. Elles présentent aussi des difficultés de remplacement, dans le sens où la multiplication des copolymères utilisés rend leur remplacement plus complexe. Le cas du plastique est intéressant car une partie de l'industrie plastique est située au Texas qui vient d'essuyer des conditions météorologiques difficiles. Il y a eu un effet domino. Les prix des matières plastiques ont alors augmenté. Nous ne sommes pas à l'abri d'autres événements de ce genre.
Un problème va certainement se poser aussi pour les cartes électroniques nues. Le circuit est pré-imprimé avec un feuillard de cuivre et ce feuillard est similaire à celui qui est utilisé pour les batteries lithium-ion. On risque d'avoir un souci d'arbitrage des capacités de production entre les cartes et les batteries....
Savez-vous s'il y a des projets de relocalisation qui concernent la production de semi-conducteurs?
Les semi-conducteurs s'obtiennent par un procédé de photolithographie et la difficulté consiste à imprimer avec la bonne résolution. Les procédés les plus à la pointe ne sont pas en Europe. Les Coréens ou les Japonais ont des procédés d'une précision de l'ordre de 5 nanomètres. En Europe, nous ne passons pas en-dessous des 26 nanomètres actuellement. Il faut faire venir la production à nous. Il s'agit donc plus de transfert de compétences que de relocalisation.
La relocalisation est un concept séduisant mais on va se heurter à trois problèmes que sont l'expertise - on vient d'en parler -, les délais - il faut un à deux ans pour monter une usine - et les investissements, qui sont conséquents.
Les constructeurs européens pourraient-ils envisager de créer une JV pour financer la création d'une usine de semi-conducteurs?
Pour certains composants, je dirais pourquoi pas, mais pour les semi-conducteurs, je réponds, sans doute pas. L'industrie automobile est une industrie manufacturière de gros volumes mais pas nécessairement avec de fortes marges unitaires. L'industrie des semi-conducteurs fonctionne à l'inverse, elle est très capitalistique avec des tickets d'entrée élevés et des temps d'amortissement longs. Les Taiwanais veulent faire une nouvelle usine : ils mettent 20 milliards de dollars sur la table... un chiffre à mettre en relation avec le montant des bénéfices qu'un constructeur peut dégager. C'est un scenario intellectuellement intéressant mais il y a une vraie dissonance entre les deux industries. L'industrie automobile est aujourd'hui très centrée sur l'électrification, qui consomme déjà beaucoup de ses ressources. Intégrer verticalement de nouveaux composants poserait un problème d'arbitrage, pas impossible mais improbable.
Que conseillez-vous actuellement à vos clients impactés par la crise des semi-conducteurs ou autre pénurie?
Au premier chef, de travailler sur la nomenclature de leurs produits. Actuellement, l'analyse des risques achats est souvent faite sous l'angle d'une analyse par famille d'achats, en provenance soit de Pareto, soit d'analyse de risques basées sur les commodités. Je pense que ce n'est pas un angle approprié. Il faut d'avantage s'interroger sur les produits sur lesquels l'entreprise a le plus d'enjeux. Il est moins "gênant" d'être en rupture de stock sur un produit qui apporte peu de marge et d'image que sur un produit plus impactant pour l'activité de l'entreprise. Il faut descendre tout en bas de la nomenclature du produit et non de la nomenclature achat.
Si vous voulez tirer une conclusion de cette crise, peut-être que l'angle d'approche est de mieux rendre visible le lien entre ce que je veux vendre et ce que je dois acheter, et de rendre cette gestion plus dynamique ?
Lire l'étude KPMG, cliquer ici
Sur le même thème
Voir tous les articles Performance